Antibacterial injection molding technology Product information 12/05/2022
Antibacterial plastic injection molding technology is one of the modern technologies used in the production of plastic products for the medical industry. This technology offers significant benefits for both manufacturing and consumption. The following information will help you understand more about the plastic injection molding technology used in the production of plastic products in general and medical plastics in particular.

Antibacterial injection molding technology
Overview of medical plastic injection molding technology
Nowadays, plastic products are becoming increasingly diverse, with various styles and sizes, including consumer plastics and antimicrobial plastics for the healthcare industry. This is the outcome of production operations utilizing the injection molding technology. So, what is injection molding technology? How does the formation process take place?
Injection molding technology and its historical development
According to the website of Advance Cad Technology Center: “Injection molding is a manufacturing technology that involves injecting molten material into a mold. The injection molding process can be applied to various types of materials, such as metals, glass, elastomers, and composite materials, but the most common ones are thermoplastic and thermosetting plastics. The material is fed into a heated barrel, mixed (using a screw system), and injected into the mold, where it cools and solidifies into the shape of the mold cavity. Combined with additional post-processing steps, it produces a complete injection-molded plastic product.”
The United States is considered the “birthplace” of injection molding. In 1872, two brothers, John Wesley Hyatt and Isaiah, invented the injection molding machine based on the principle of a large syringe. Using a piston, the plastic material is heated and pumped into the mold through a cylinder.
In 1903, German scientists Arthur Eichengrün and Theodore Becker discovered forms of cellulose acetate that were more soluble and less flammable than cellulose nitrate, making them suitable for injection molding. In 1939, Arthur Eichengrün developed the first injection molding machine and was granted a patent for the mold for flexible cellulose acetate plastic.
In 1946, James Watson Hendry, an American inventor, created the first screw injection molding machine, which allowed for more precise control of injection speed and product quality. In 1970, he developed the first gas-assisted injection molding system, which facilitated rapid cooling of complex products. In the 1990s, aluminum molds became widely used. Nowadays, screw pumps dominate the majority of plastic injection molding machines.

Medical Plastic Injection Molding Machines at Rang Dong HealthCare
Application of Antimicrobial Medical Plastic Injection Molding Technology
Plastic injection molding technology is applied to the production of various plastic products. These include everyday consumer plastics, auxiliary plastic materials for industries such as electronics, automotive, and other machinery. Particularly, the application of plastic injection molding technology is used to produce antimicrobial medical plastic products used in hospitals, clinics, and healthcare centers.
Plastic injection molded products used in the healthcare industry undergo antimicrobial processing through each stage. From the selection of raw materials to the injection molding process and final production, strict quality control measures are implemented before they are released into the market. Some prominent medical products using injection molding technology include surgical basins, positioning trays for wires, specimen containers, solution containers, bedpans, rectal immersion basins, emesis basins, and medication cups.

Application of Injection Molding Technology in Medical Plastic Product Manufacturing
Structure and Operating Principle of Medical Plastic Injection Molding Machine
Máy ép phun nhựa là thiết bị quan trọng trong công nghệ ép phun các sản phẩm nhựa y tế. Thiết bị này có cấu tạo và hoạt động như thế nào?
Structure of Plastic Injection Molding Machine
A plastic injection molding machine is composed of five components: the clamping system, the injection mold, the injection system, the hydraulic system, and the control system.
- Clamping System: It is a unit that has translational motion. Its function is to open and close the mold, assist in the movement of mold components, and provide the clamping force.
- Injection Mold: It consists of a stationary mold half and a movable mold half. The stationary mold contains the cavity, while the movable mold carries the core. Cooling systems and runner channels are arranged within the mold.
- Injection System: The injection system consists of four main components: the material hopper, the heating cylinder, the screw, and the nozzle. The material hopper holds the plastic material. The heating cylinder heats and melts the plastic material. The screw is divided into three sections: the feeding section, the compression section, and the metering section. The nozzle is attached between the end of the heating cylinder and the sprue of the injection mold. Different nozzle structures optimize the process of injecting plastic into the mold.
- Hydraulic System: It provides the energy for opening and closing the mold, applying clamping force, rotating the screw, and generating the ejection force for mold separation.
- Control System: This system displays and controls various parameters during the plastic injection process, directly influencing the quality of the final product.
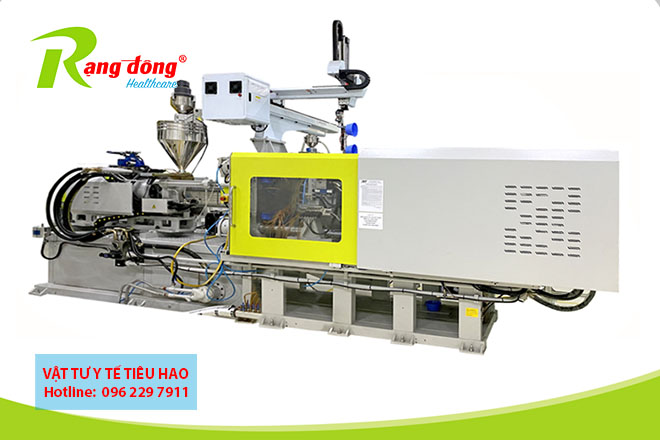
Plastic injection molding machine
Principles of Producing Antimicrobial Medical Plastic Products
The plastic injection molding machine used for producing antimicrobial medical plastic products operates primarily through the following 4 basic steps.
- Step 1: Clamping. The hydraulic clamping unit pushes the two halves of the mold together and holds them tightly, preparing to inject the plastic material into the mold.
- Step 2: Injection of plastic material. The raw plastic material in pellet form is fed into the injection molding machine. Under heat, it melts and is injected into the mold held by the hydraulic clamping unit.
- Step 3: Cooling. The molten plastic, after being injected into the mold, comes into contact with the inner surface of the mold and gradually cools and solidifies into the shape of the product. Attention is given to the cooling time to prevent any potential shrinkage of the product.
- Step 4: Ejection of the finished product. After the cooling time, the ejection system pushes the product out of the mold and continues the production cycle for the next product.
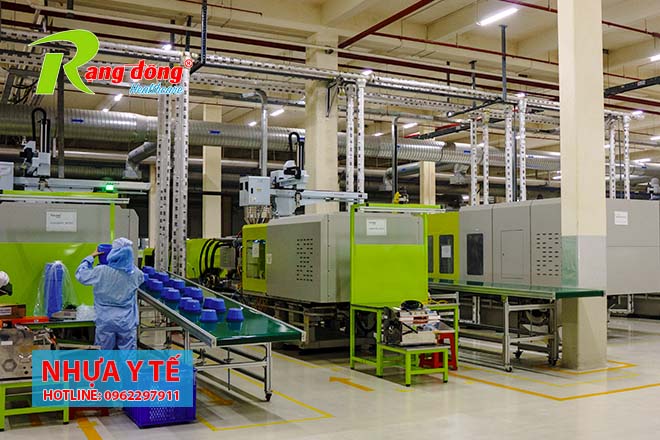
Injection Molding Machine at Rang Dong HealthCare Medical Plastic Factory
Advantages and Disadvantages of Producing Medical Plastic Products using Injection Molding Technology
Every manufacturing technology has its advantages and disadvantages. Similarly, the injection molding technology for producing medical plastic products also has its own set of advantages and disadvantages that you should be aware of.
Advantages
The injection molding technology can produce a wide range of products, from simple to complex, in the medical plastic industry. Examples of such products include surgical trays, medication vials, specimen containers, and syringe pumps.
One of the key advantages of injection molding is its fast production speed. Plastic products can be rapidly cooled, allowing for high production volumes. With just one machine and one operator, hundreds of products can be produced within a minute.
Medical plastic products manufactured using injection molding technology exhibit high antimicrobial properties. During the injection molding process, the plastic materials undergo careful thermal treatment to ensure their cleanliness and sterility.
Quality control is easily maintained throughout the production process. Molded products can incorporate labels and engraved logos, ensuring clear and consistent product origin and branding.
Disadvantages
Every manufacturing technology has its advantages and disadvantages. Injection molding technology used in the production of medical plastic products has the following drawbacks: certain designs cannot be molded or are difficult to mold, high initial investment costs (including technology, machinery, and mold), and time-consuming mold design process.
However, during the production of medical plastic products using injection molding technology, these drawbacks can be overcome through various methods. The appropriate methods are applied based on practical situations.

Plastic Injection Molding Machine Operators at Rạng Đông HealthCare
Medical Plastic Products Manufactured using Injection Molding Technology by Rạng Đông HealthCare
Rạng Đông HealthCare produces a wide range of medical plastic products using injection molding technology. Our technology and production processes are verified to meet US standards, ensuring antimicrobial properties. The products we manufacture are widely used in operating rooms, ICUs, and other hospital departments. In addition to supplying the domestic market, Rạng Đông HealthCare also exports to international markets such as the United States, United Kingdom, Canada, and more.
Below are some medical plastic products produced by Rạng Đông HealthCare using antimicrobial injection molding technology.

Antimicrobial Medical Plastic Cups

Non-Sterile Solution Container

Specimen Sample Box
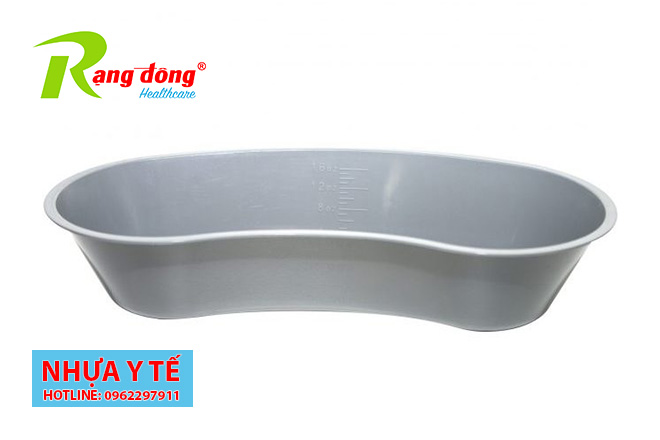
Medical Emesis Basin

Non-Sterile Surgical Basin

Patient Bedpan
- Factory address: Lots G4-G8, Street No. 8, Tan Do Industrial Park, Long An Province.
- Hotline: 096 229 7911 (Mr Duy Triển)
References for the article:
- Website of Advance Cad Technology Center
- Website of Nam Lam Mechanical Engineering
Tags: công nghệ ép phun, công nghệ ép phun nhựa, sản phẩm nhựa y tế ép phun, ép phun sản phẩm nhựa y tế, máy ép phun nhựa, công nghệ ép phun là gì, rạng đông healthcare, nhựa y tế rạng đông healthcare